OT – IT for Operational Twin
A mature digital twin encompasses both operational technology (OT) and information technology (IT) domains. Harmonised operation of both domains is crucial for digital twin functionality and integration of both domains, preferably based on standards.
The actual control of physical systems is managed through a category of systems in the operational technology (OT) domain. At its core is the milliseconds- and seconds-based measured process parameter and actuator process controller monitoring. If used as part of, or directly linked to model-based control solutions, OT systems are part of a digital twin (De Leeuw’s Paradigm).
De Leeuw's control paradigm (De Leeuw 1974)
The paradigm of control of de Leeuw is based on the theory of systems. It first describes the main concepts of the system theory of control: the so-called Controller and the Controlled system. The Controlled system is the system that has to be controlled in one way or another. The Controller does not only get input from the Controlled system but also from the wider Environment. The Controlled system can provide output to the Environment and be influenced by it.
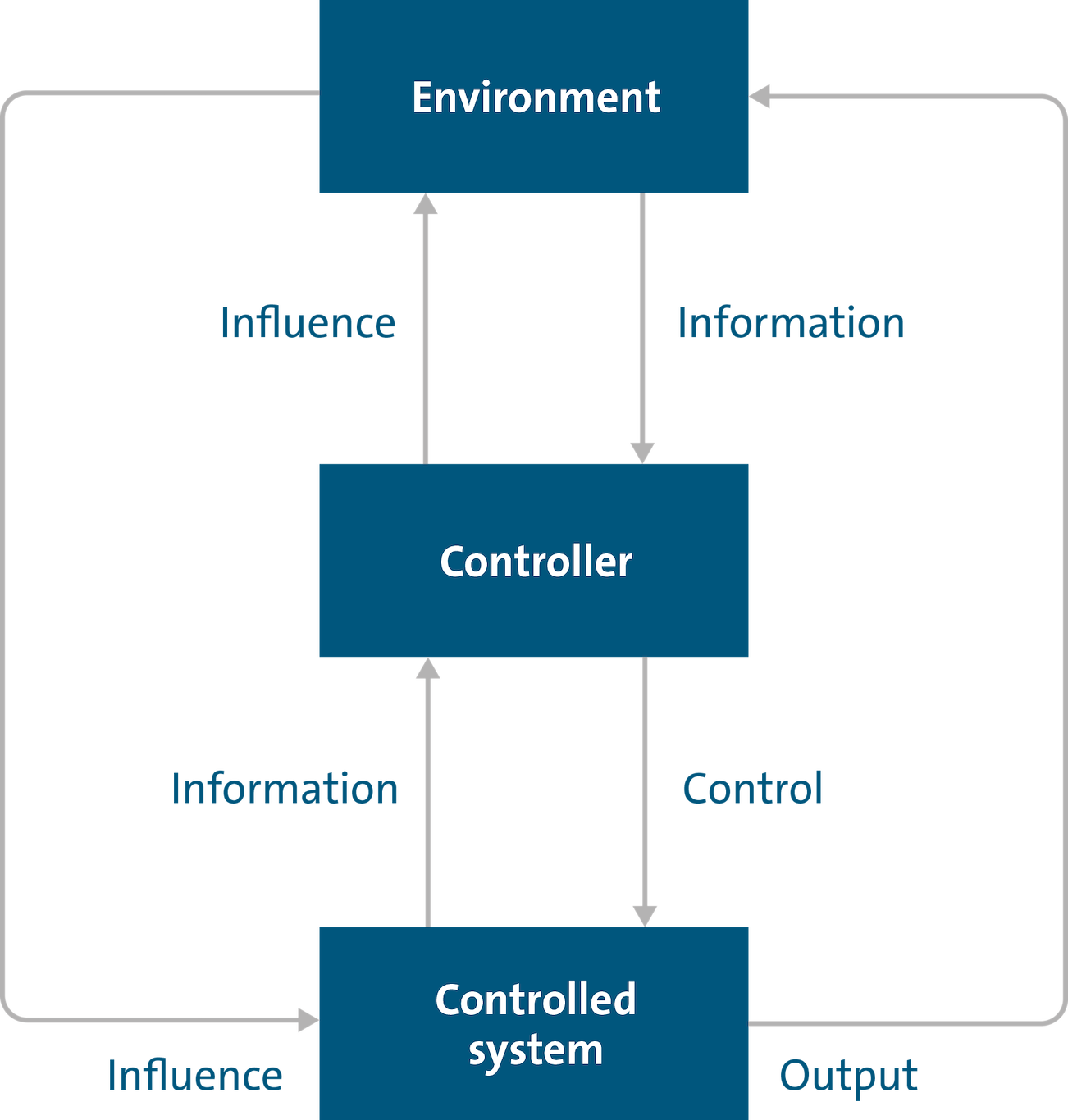
The importance of the paradigm in the context of digital twins is the positioning of the digital twin. The digital twin can be embedded in the Controller as a model-based controller. How depends on the actual requirements. Sometimes embedding (part of) it in the (milli)seconds based OT system is required. In other situations and for other purposes, putting it on top of the OT system is more appropriate. Hybrid solution directions are also possible.
Other models that are part of a digital twin in the IT domain operate with longer intervals (minutes, hours, or days). For operational data, IT domain systems typically depend on data collected in the OT domain, traditionally through Distributed Control Systems (DCS) or Supervisory Control and Data Acquisition (SCADA) systems. But increasingly, this data can also be collected by other systems, for example, directly from industrial internet of things (IIoT) sensors.
In general, OT domain system requirements are different from IT domain systems. That’s because the consequences of OT systems being unavailable for a given period – or even worse, being taken over after being hacked – can be severe.
The relationship between OT and IT domains is described in the S95 standard (ISO-62264).
The S95 (ISO-62264) standard
Important and commonly referenced elements of S95 are the hierarchy model (with five levels) and the generic activity model.
As S95 is focused on manufacturing operations, the generic activity model is considered applicable for production, maintenance, inventory, and quality-related operations. The generic model can also be used for operations related to other aspects, like health, safety, security and environment (HSSE), and sustainability.
While digital twin functionality can be executed in either of the two domains, choosing where to execute specific functions depends on parameters like cyber security, interface requirements, system maintenance approach, system availability requirements, and choices made by solution vendors.
Split and interaction between OT and IT domains
A natural split between the OT and IT domains is between levels two and three in the S95 hierarchy model, with generic activity model functions executed in level three and the interface between the OT and IT domain implemented based on a standard interface like OPC-UA. But this isn’t always the case, as is shown in the solution approach example below where the OT system is required to function independent of the level three system in the IT domain.
Developments like the Open Process Automation Forum (OPAF) will impact how OT and IT will integrate and work together (see Open Process Automation™ Forum | The Open Group Website).
ISA 95 piramide characteristics
In this drawing the characteristics on functions, time behaviour and involved systems are visualised.